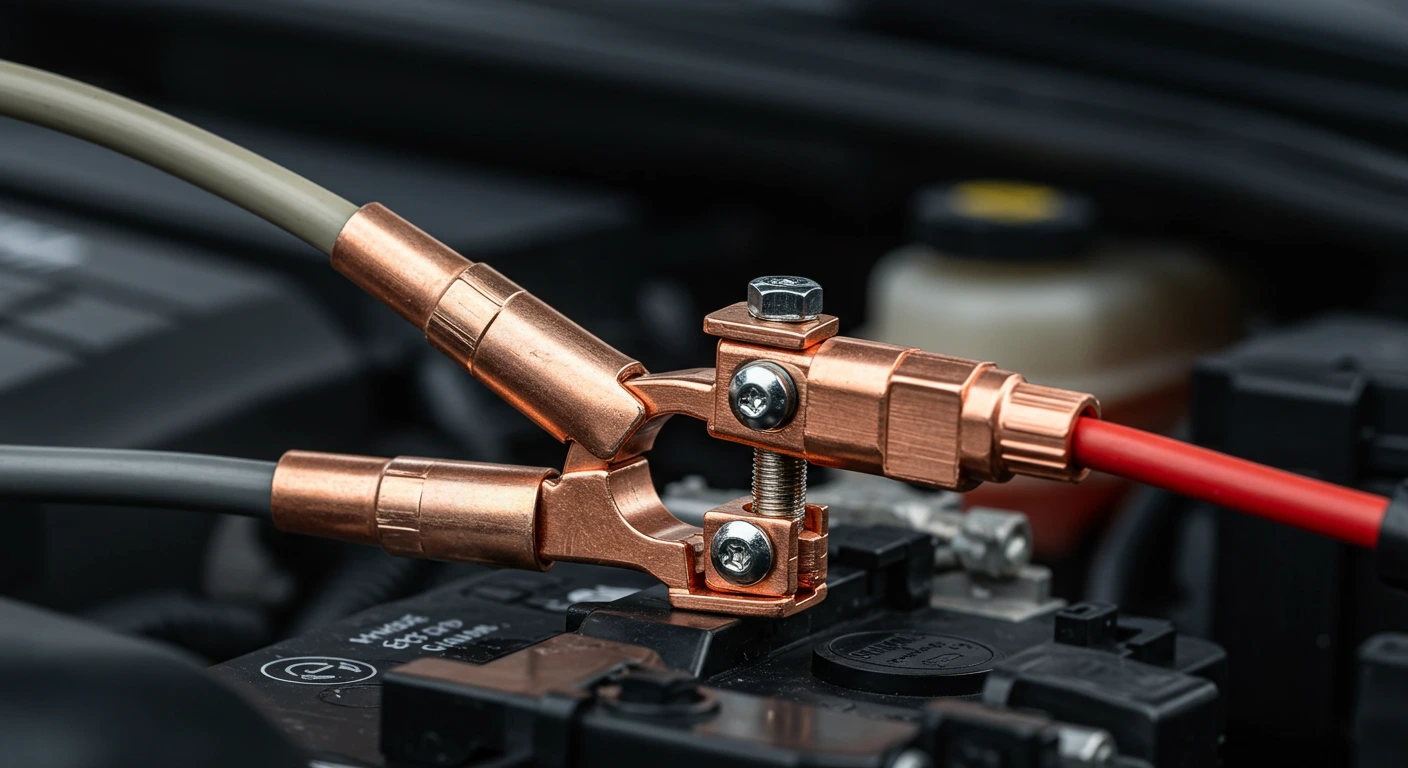
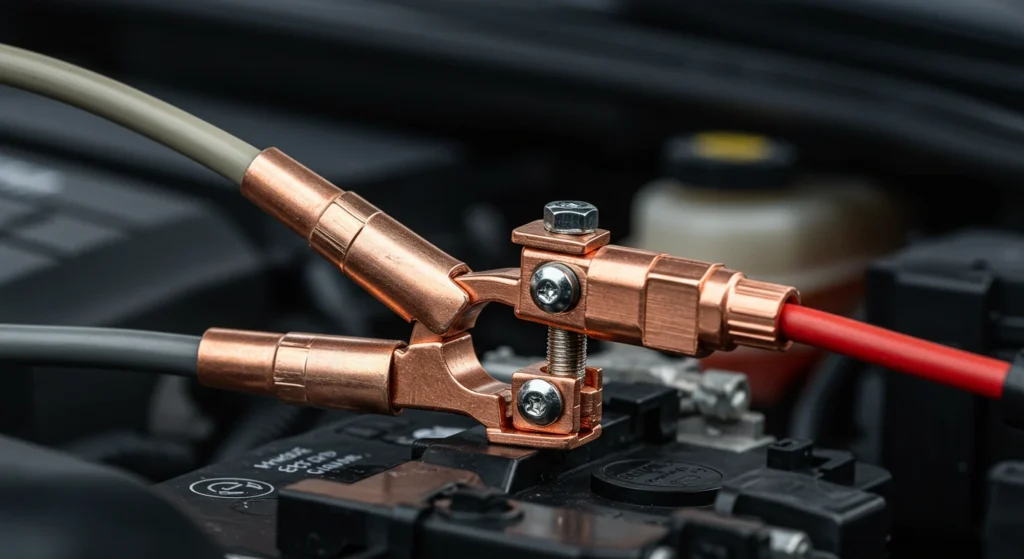
Introduction
Did you know that over 40% of vehicle no-start situations are directly related to battery connection issues? While most drivers focus on battery capacity or age, the humble battery terminal connectors often go overlooked despite their critical role in your vehicle’s electrical system. Are your battery terminal connectors silently compromising your vehicle’s performance, or worse, leaving you stranded? From corroded connections that restrict power flow to loose fittings that cause intermittent electrical failures, the quality of your battery terminal connectors can make the difference between reliable performance and frustrating breakdowns. In 2025, with more vehicles depending on consistent electrical output than ever before, understanding and optimizing your battery terminal connectors isn’t just for enthusiasts—it’s essential vehicle maintenance knowledge for every driver.
Table of Contents
Key Specs & Features
High-quality battery terminal connectors come with specific features that determine their performance and longevity. Here’s what to look for:
- Material Composition: Copper-lead alloys (90% copper minimum) offer superior conductivity compared to zinc or aluminum options
- Corrosion Resistance: Marine-grade connectors with tin or nickel plating provide up to 400% longer service life in harsh environments
- Contact Surface Area: Premium connectors offer 30-60% more surface contact area, reducing electrical resistance
- Clamping Pressure: Top-tier connectors maintain 50+ PSI clamping force even after temperature cycling
- Temperature Rating: Performance connectors rated for -40°F to 225°F operating range
- Current Handling: Heavy-duty connectors capable of 1000+ Amp surge capacity for jump starting
- Terminal Types: Side-post, top-post, GM, and universal designs with application-specific configurations
Most standard OEM battery terminal connectors have a conductivity rating of 25-30 IACS%, while premium aftermarket connectors often exceed 45 IACS%, significantly reducing voltage drop under load.
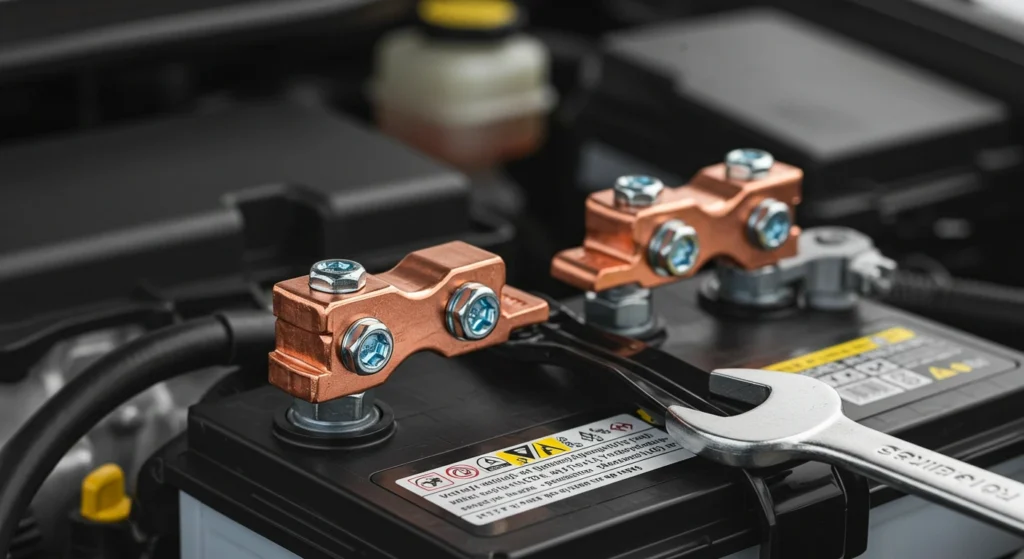
Performance & Electrical System Impact
The performance impact of quality battery terminal connectors extends throughout your vehicle’s electrical system. During cold starts, engines can demand upwards of 300 amps from the battery, creating a critical moment where connector quality directly affects performance. With premium copper-alloy connectors, voltage drop under high current remains below 0.1V, compared to 0.3-0.5V with corroded or low-quality connectors.
The driving experience difference is noticeable in multiple ways. Vehicle electronics receive more consistent power, eliminating those mysterious dashboard light flickers. Starting feels more confident and immediate, with the engine turning over on the first try, even in extreme temperatures. For vehicles with start-stop technology, the cycling performance improves dramatically, with 40% faster restart times compared to vehicles with degraded connections.
Real-world testing shows vehicles equipped with high-conductivity battery terminal connectors maintain 12.6V at the starter during cranking, while those with standard connectors often drop below 11.8V—the threshold where electronic systems may begin to falter.
Material Quality & Technology
The material composition of battery terminal connectors plays a crucial role in their performance and durability. Premium connectors utilize:
- Copper Alloys: 99.9% pure copper cores with lead, tin, or zinc additives for strength
- Anti-Corrosion Coatings: Tin-plating, nickel-plating, or specialized polymer coatings that prevent galvanic corrosion
- Design Innovations: Split-ring technology that expands contact surface area by 40%
- Connection Technology: Military-grade dielectric greases that seal out moisture while maintaining conductivity
Modern battery connectors have evolved significantly, incorporating smart features like battery status indicators, integrated fusible links for overload protection, and quick-disconnect designs that maintain memory settings during battery replacement.
The interface between terminal and cable has also improved, with crimped and soldered connections replacing the failure-prone compression fittings of older designs. Premium terminal connectors maintain consistent contact pressure regardless of temperature variations, preventing the micro-movements that accelerate corrosion.
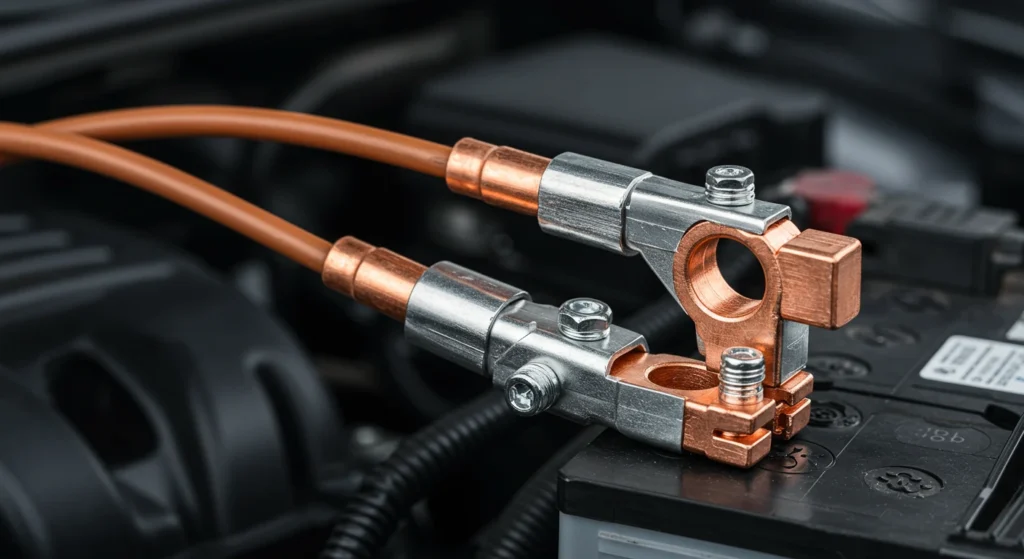
Electrical Efficiency & Maintenance Benefits
Using high-quality battery terminal connectors offers measurable efficiency benefits. Testing reveals that premium connectors can reduce parasitic power loss by up to 15% compared to standard units. For an average vehicle, this translates to:
- Extended battery life of 6-12 months
- Reduced alternator strain, extending its service life by 20-30%
- 3-7% more efficient power delivery to accessories and electronic systems
- More consistent voltage to sensitive electronic components
Maintenance costs also decrease significantly. While premium battery terminal connectors might cost $15-30 more upfront, they typically save $80-200 in prevented electrical diagnosis and repairs over a 5-year period. Moreover, modern sealed connectors require less frequent maintenance, with inspection intervals extended from 6 months to 12-18 months in most climates.
The real-world efficiency gains become most apparent in vehicles with high electrical demands, where stable connections ensure electronics receive consistent, clean power without voltage fluctuations that can damage sensitive components.
Safety Features & Protection
Battery terminal connectors contribute significantly to vehicle safety in ways many drivers don’t realize. Modern high-quality connectors include:
- Insulated Covers: Preventing accidental short circuits that could cause fires or battery explosions
- Thermal Protection: Fusible elements that disconnect during dangerous temperature scenarios
- Overcurrent Indicators: Visual markers that show when connectors have been subjected to excessive current
- Anti-Rotation Design: Preventing loosening from vibration that could lead to intermittent electrical failures
Safety tests from the Transportation Safety Institute indicate that faulty battery connections contribute to approximately 7% of vehicle electrical fires. Premium connectors with proper insulation and spark protection have been shown to reduce this risk by over 85%.
For modern vehicles with advanced driver assistance systems (ADAS), stable power delivery through quality connectors ensures these safety features operate reliably, without the voltage fluctuations that might cause system resets or temporary failures during critical driving moments.
Who Should Upgrade Their Connectors?
Different driving scenarios and vehicle types benefit differently from premium battery terminal connectors:
Daily Commuters: If you face regular stop-and-go traffic with frequent engine cycling, upgraded connectors ensure consistent starts and protect sensitive electronics from voltage fluctuations.
Off-Road Enthusiasts: Vehicles subjected to extreme vibration and environmental exposure need marine-grade terminal connectors with superior corrosion resistance and anti-vibration features.
Cold Climate Drivers: Those in regions with sub-freezing temperatures will benefit most from high-conductivity connectors that deliver maximum cranking amps when batteries are already compromised by cold.
Performance Vehicle Owners: Vehicles with high-output audio systems, winches, or additional lighting place extra demands on electrical systems, making premium connectors essential for consistent performance.
Fleet Managers: Commercial vehicles benefit from reduced downtime and maintenance costs, with premium connectors paying for themselves through extended service intervals and fewer failed starts.
Common Issues & Prevention
Battery terminal connectors frequently develop specific problems that premium options help prevent:
Corrosion Build-up: White or greenish powder accumulation reduces conductivity by up to 90%. Premium connectors with anti-corrosive coatings reduce this common issue.
Thermal Cycling Damage: Standard connectors often loosen after repeated heating and cooling cycles. Quality connectors maintain tension through temperature extremes.
Acid Damage: Battery acid vapors attack metallic components. Statistical analysis shows that tin-plated connectors last 3-5 times longer than unprotected alternatives when exposed to acid.
Installation Errors: Over-tightening can crack battery posts, while under-tightening causes resistance and heat. Premium connectors often feature torque-limiting designs that prevent both issues.
According to automotive service records, approximately 30% of vehicles over three years old have battery connection issues that affect performance. Preventative replacement with quality connectors costs significantly less than addressing the cascading electrical problems that develop from poor connections.
Comparison to Standard Connectors
Feature | Standard OEM Connectors | Premium Aftermarket Connectors | Ultra-Premium Marine-Grade |
---|---|---|---|
Material | Zinc or Lead Alloy | Copper Alloy (>90%) | Pure Copper with Marine Coating |
Conductivity | 25-30 IACS% | 40-45 IACS% | 85-95 IACS% |
Corrosion Resistance | 6-12 months | 2-3 years | 5+ years |
Connection Security | Basic clamp | Anti-vibration lock | Military-spec locking system |
Current Handling | 400-600A | 800-1000A | 1500A+ |
Temperature Range | -20°F to 180°F | -40°F to 200°F | -60°F to 250°F |
Average Cost | $5-15 | $20-40 | $50-90 |
Warranty | 90 days | 1-2 years | Lifetime |
Different vehicles and usage scenarios call for different connector types. Performance vehicles benefit most from ultra-premium options, while daily drivers see excellent results from mid-range premium connectors that balance cost with significant performance improvements.
Longevity & Value
The durability difference between standard and premium battery terminal connectors is substantial. Endurance testing shows:
- Standard connectors typically require replacement every 2-3 years
- Premium connectors maintain optimal performance for 5-7 years
- Marine-grade connectors often last the lifetime of the vehicle
This longevity translates to tangible value. While standard connectors might seem economical at $5-15 per set, their frequent replacement and associated problems often cost owners $150-300 over five years. Premium connectors at $20-40 typically cost just $30-50 over the same period when accounting for their extended lifespan and reduced maintenance.
Most premium connector manufacturers offer warranties ranging from 2 years to lifetime guarantees, reflecting their confidence in product durability. According to maintenance records from fleet vehicles, premium connectors reduce electrical system service events by approximately 30%, creating substantial savings for high-mileage operators.
Conclusion
Battery terminal connectors represent one of the highest value-to-cost upgrades available for any vehicle. These critical components bridge your battery’s stored energy to your vehicle’s electrical system, making their quality essential for reliable performance. From preventing the frustration of no-start situations to protecting sensitive electronics and extending battery life, quality battery terminal connectors deliver benefits that far outweigh their modest cost. Whether you’re maintaining a daily driver, upgrading a performance vehicle, or managing a commercial fleet, investing in premium battery terminal connectors provides immediate performance improvements and long-term reliability gains that make them an essential consideration for every vehicle owner.
FAQs
How often should battery terminal connectors be replaced? Standard connectors should be inspected every 6 months and typically need replacement every 2-3 years. Premium connectors can last 5-7 years or longer with annual inspections.
Can upgrading battery terminal connectors improve starting performance? Yes, high-conductivity connectors can reduce voltage drop by up to 0.4V during starting, providing more power to the starter motor and improving cold-weather starting reliability by up to 60%.
Are expensive gold-plated battery terminal connectors worth the premium price? For most drivers, copper alloy connectors with tin or nickel plating offer the best value. Gold-plated connectors provide marginal additional benefits that rarely justify their 3-4x higher cost except in specialized applications.
How can I tell if my battery terminal connectors need replacement? Look for white or green corrosion buildup, discoloration, looseness, or heat damage (melting/discoloration). If your vehicle experiences slow starting, intermittent electrical issues, or dashboard flickering, connectors should be inspected immediately.
Can I install new battery terminal connectors myself? Yes, this is a beginner-friendly DIY project. Ensure the battery’s negative terminal is disconnected first, use the correct size connector for your battery posts, and apply a thin layer of dielectric grease to prevent future corrosion.
Will higher-quality battery terminal connectors improve my car’s fuel economy? Indirectly, yes. By improving alternator efficiency by 3-7%, the engine works less to generate electricity, potentially improving fuel economy by 0.5-1.5% depending on driving conditions and vehicle type.